A laser cutting machine‘s core components include the laser source, beam delivery system, cutting head, motion control system, and CNC controller. Hindcam manufactures and assembles each element with the utmost accuracy, ensuring high precision, efficiency, and reliability during the cutting process. The laser cutting machines are available in different power ranges from 1 kw onwards and can be modified as per your business requirements.
Machine’s Overview
Technical Components for the laser cutting machines
For the flowless& intricate designing, cutting parameters set-up, and its successful implementation over the metallic material cutting. Here are the core components for the manufacturing of a laser cutting machine:
1. Laser cutting head: recommended (Raytool).
The laser cutting head (BM110/BM111) is among the main core components of the fiber laser cutting machine. It ensures that the focusing lens/focus tracking system works perfectly using its auto-focus mechanism per the material thickness level. And the laser beams fall under the correct setup area. And while performing the high-precision cutting, its cooling systems prevent overheating, and sensors ensure optimal performance by monitoring parameters such as perfect distance, required gas pressure, and correct alignment.
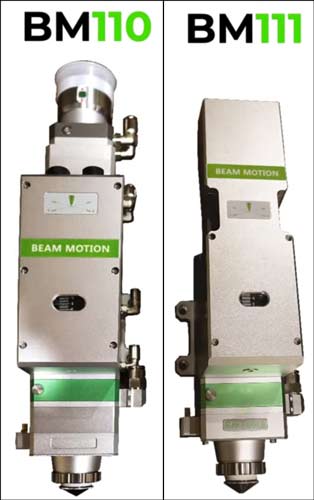
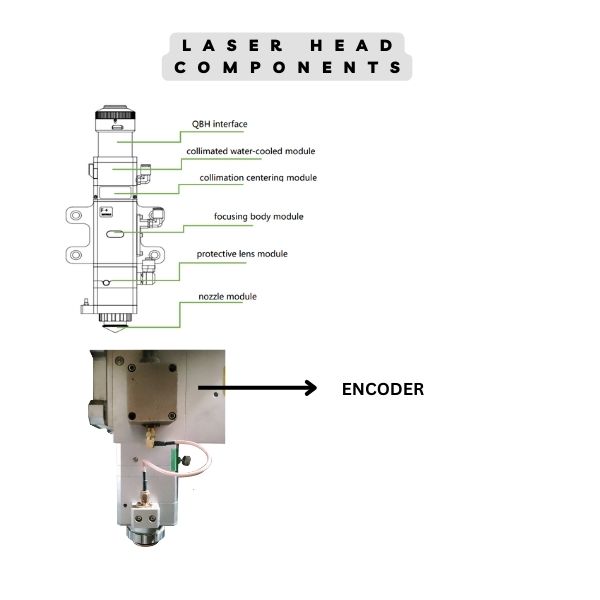
2. Laser source generator: Recommended ( Max Photonics/Raycus)
Highly efficient laser beams are emitted using the laser source generator (Max Photonics & Raycus). It enhances the cutting quality with its cutting-edge focused beam.
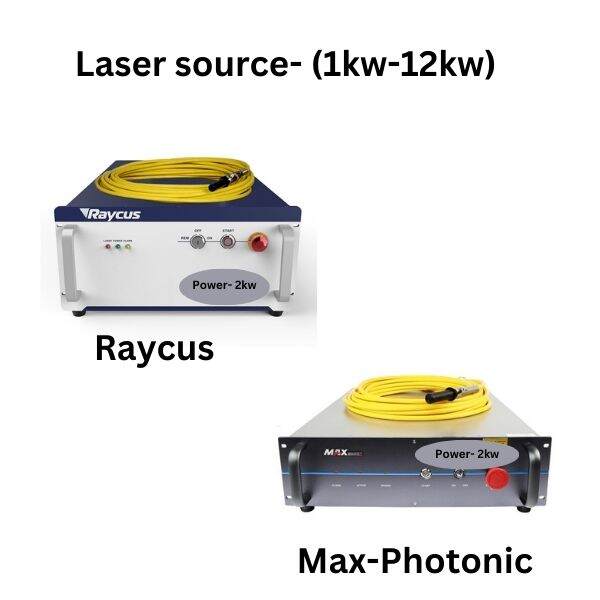
specification | Typical Value |
---|---|
Laser Power | 1.5 kw-6kw |
Wavelength | 1064nm |
Beam Quality | ≤1.3 |
Cooling Method | Water-cooled |
Efficiency | ≥30% |
Fiber Core Diameter | 50µm |
Modulation Frequency | 1-50kHz |
Voltage Input | AC 220V or AC 380V |
3. Cooling system/element:
A cooling system includes a chiller. Recommended company is S&A/Henley. It helps in reducing the overheating and prevents any wear/tear to the machine’s parts or elements. This finally results in enhanced working efficiency, safety, and sudden thermal shutdowns.
- Machine’s power: 2 kW laser cutting machine
- Cooling Capacity: 10 kW
- Temperature Control Precision: ±0.3°C
- Flow Rate: 30 LPM
- Power Supply: 380V/50Hz
- Refrigerant: R-410a
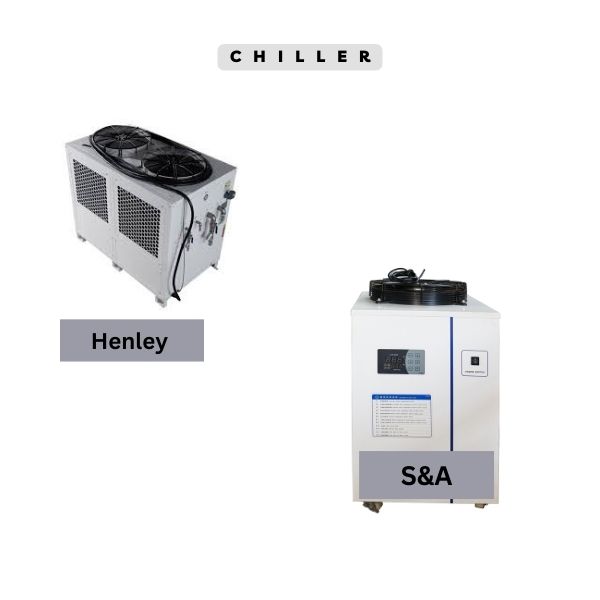
4. Servo motor/Stepper motor: Recommended (Yaskawa/Innovance/Delta/Fuzi)
Both the servo motor and stepper motor help in smooth laser cutting head movement along the X, Y, and Z axes.
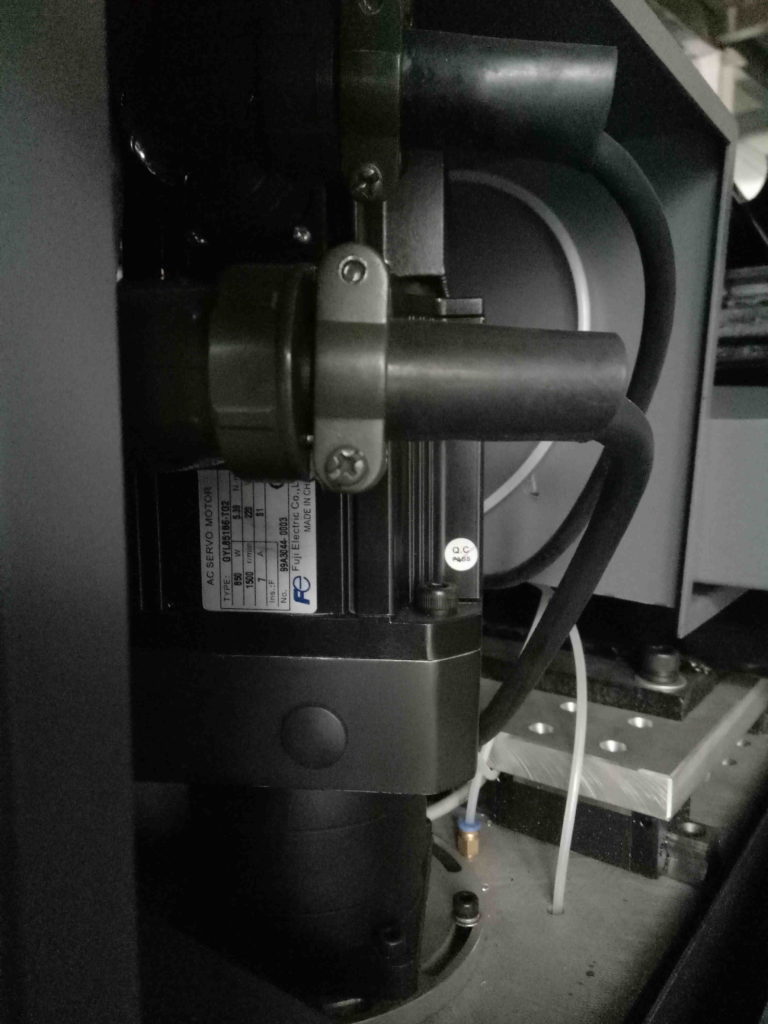
Comparison: Servo motor VS Stepper motor
Feature | Servo Motor | Stepper Motor |
---|---|---|
Precision | Extremely High | Moderate |
working mechanism | electric servo mechanism | DC motor/shaft rotation |
Speed | Very High | Moderate |
Power consumption | less power | more power |
Feedback | Closed-loop system | Open-loop system |
Designing | Complex | Simpler |
Load Capacity | Handles heavy loads | Limited load capacity |
Cost | Higher | Lower |
5. Air Compressor: screw, 16bar
A screw air compressor with a 12-16 bar pressure is capable of supplying high-pressure, clean, and dry air as an assist gas. And it works as an anti-oxidant for the highly reflective metal surface. And thus fulfills the excellent cutting performance followed by the reduced cutting cost. Also, with the compressed air technique, we can cut a wider range of materials.
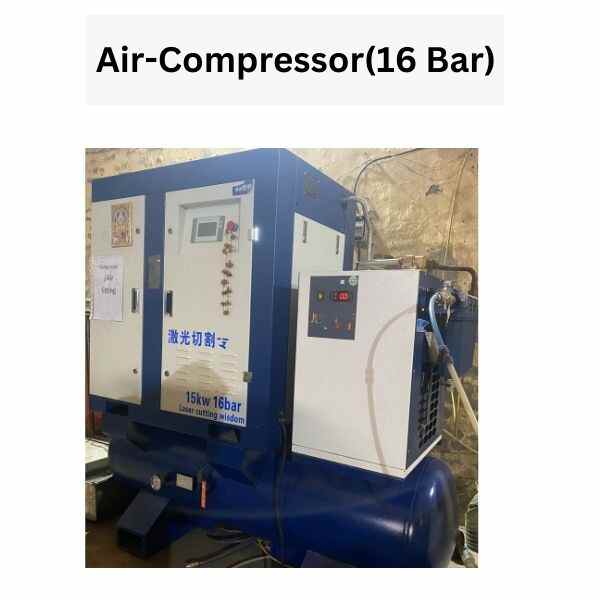
6.CNC Digital Control Panel
By using the updated version of Cypcut 2000, we can create complex designs. It has a great user interface for the parameter setups, cutting speed, gas pressure, thickness level, depth controls, and much more. As well as supporting CAD/CAM for the designing and its implementation during the cutting parmeter set-ups. Additionally, it supports machine control software (Mach3, RDWorks, &Nesting Software. It has inbuilt sensor integration and alerts for the Fault Detection, allows remote access, and has automation support.
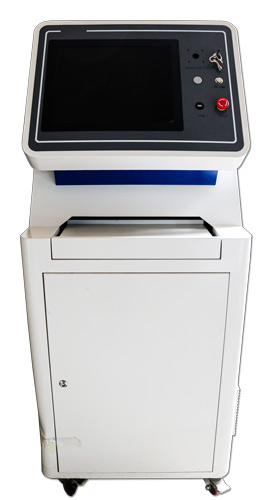
7. Motion Control System- X,Y,Z Axis
The Motion Control System is a CNC-controlled system that controls movement of the cutting head along the X, Y, and Z axes. Its rack and pinion system helps in the head’s movement into high-accuracy, high-precision by using the Gcode instructions. Its advanced features include real-time feedback and acceleration optimization for highly efficient cutting accuracy.
8. Laser-cutting head Lens
Usually, we use two types of laser cutting lenses: collimating lenses and focusing lenses. The purpose of the collimating lens is to divert the laser beam into a parallel (collimated) beam during the cutting operations.
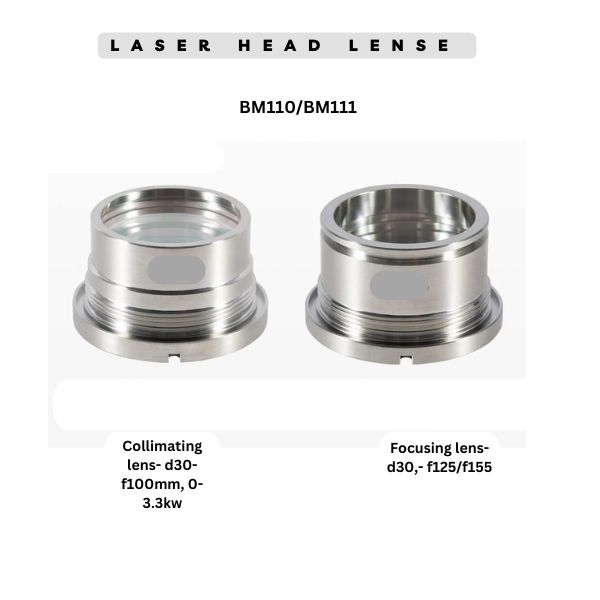
9. Connectors & Power supply
Power supplies(Mean Well) provide consistent power to the major components—the laser source, control system, motors, and cooling systems of the laser cutting machine. It enhances the cutting quality, saves time, and also reduces operational costs.
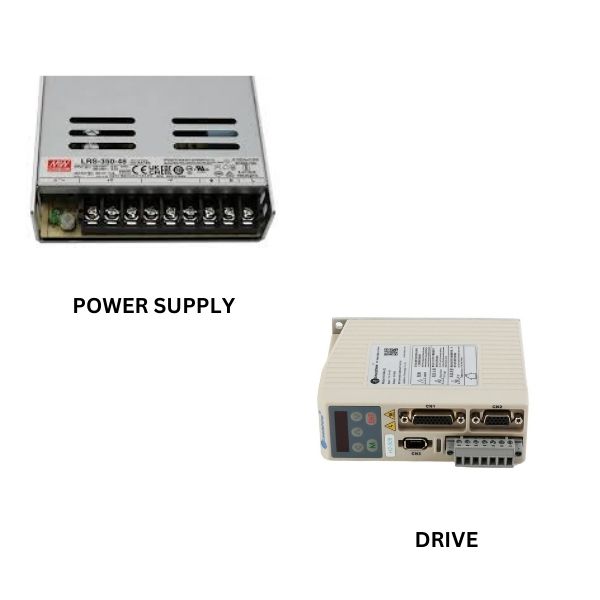
Mean Well HEP Series (For High-Power Laser Machines)
- Output Voltage: 48V DC
- Power Rating: 2000W
- Efficiency: 94%
- Cooling: Forced air cooling with a high-efficiency fan
- Protections: Overvoltage, overload, and short-circuit protection
- Input Voltage: 90-264V AC
- Dimensions: 320mm x 127mm x 42mm
10. Slag discharge machine
A slag discharge machine is used for the autoremoval of slag, debris, and waste materials during the laser cutting operations from the cutting area.
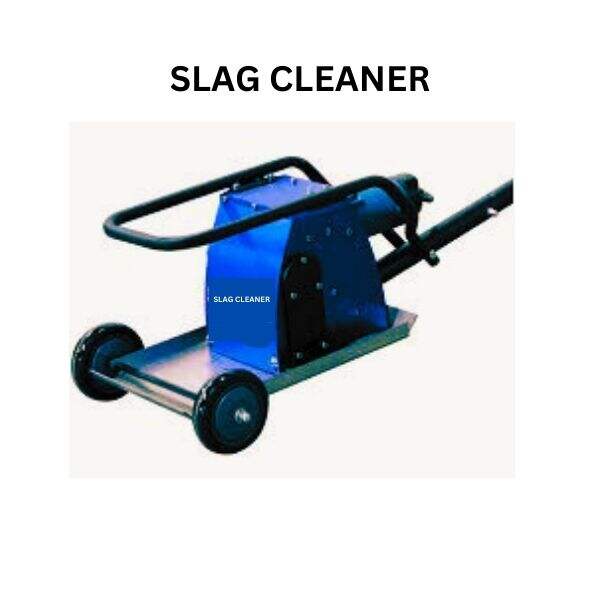
11. Nozzle
Laser head nozzels use the assist gases (oxygen, nitrogen, or air) for the cutting over the numerous metallic materials. It enhances the cutting accuracy and prevents lens.
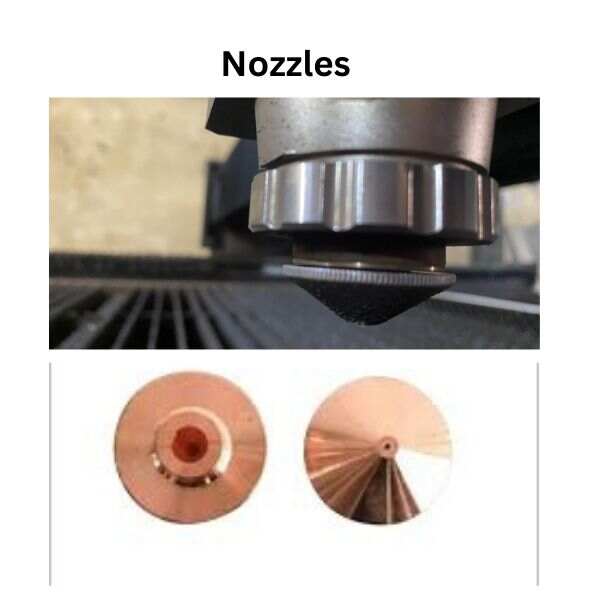
12. Dust collector and laser fumes exhactor
A dust collector/fume exhauster helps in improving the air quality and environmental cleaning. Due to the prolonged emission of metallic dust particles and harmful gaseous emissions, it can affect the health of the workers performing the laser cutting operations on the laser cutting machines. Additionally, it also improves the visibility that gets barred due to emission of fumes.
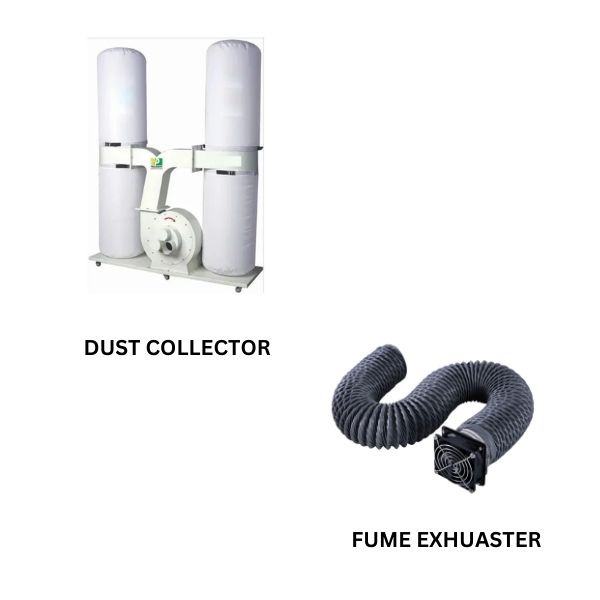
13. Cooling dryer and filters
Air dryers and filters play an important role in air purification, especially during the assisted gas cutting. It helps in improving the cutting quality and prevents corrosion and wear/damages to the tools, valves, or nozzels. It also reduces the maintenance work due to any contamination of air quality.
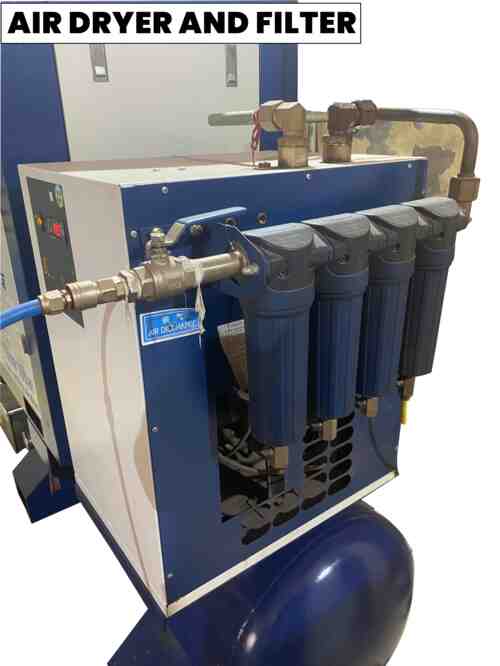
14. Uninterruptible Power Supply (UPS):
A UPS is required for the smooth operations of a laser cutting machine and prevents the unexpected and sudden shutdown of the system. So acts as a power backup source for the main components of the machine, like the CNC controller, chiller, and others.
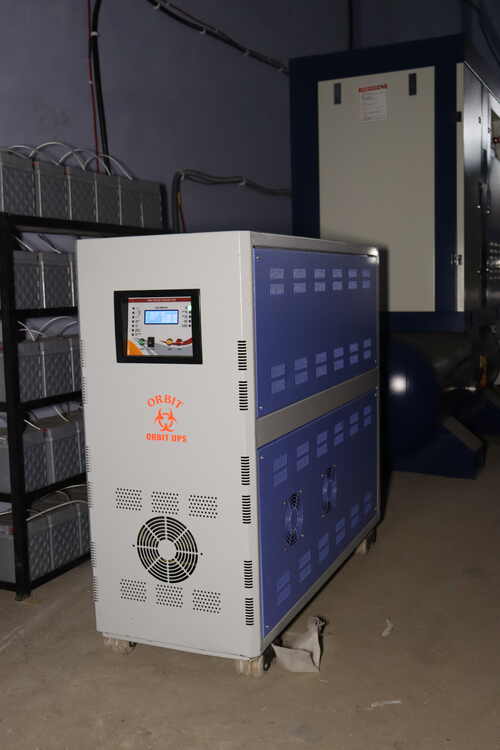
15. Laser cutting bed & Pallate changer/exchange platform
The laser cutting bed is a surface placed for smooth cutting operations and sheet holdings. It is specifically designed into multi-slats/grids so that the debris could easily fall under it. And it finally gets collected inside the tray placed underneath the cutting bed. Additionally, we should take the pallet changer (exchange platform) for sheet loading/unloading and cutting quality enhancement and minimize the cutting timing.
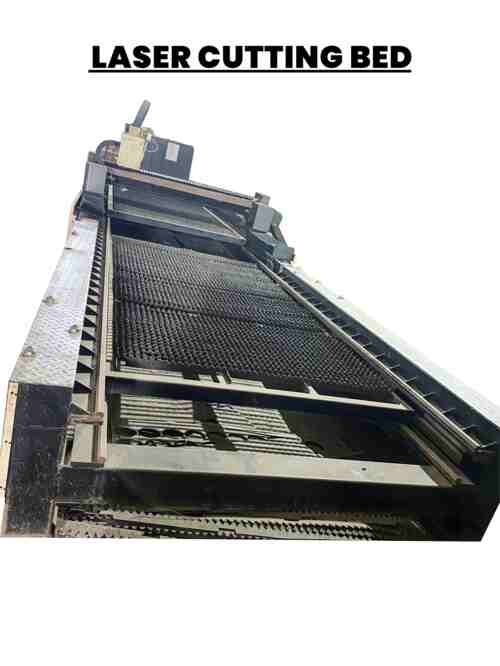
Advantages of using a Gantry-type laser cutting machine
We manufacture gantry-type laser cutting machines for the high-precision, efficient, and heavy-duty performance of multi-tasking (cutting, engraving, and designing). A gantry head moves along the horizontal laser beam supported by vertical columns.
Here are some of the advantages of using a gantry-type laser cutting machine:
- Best suited for large cutting areas and works efficiently in metal fabrication and related applicable areas.
- Works on dual side support, and the final cutting accuracy is excellent over the cutting material.
- It minimizes the laser cutting vibration and does more stable cutting operations.
- A laser cutting machine has heavy-duty performance that ensures reliability and durability in its overall working mechanism.
- It has a longer lifespan with the robust design and component integration.
- It is perfect for the heavy and large-scale manufacturing divisions in multi-applicable areas. It includes construction, aerospace, automobiles, and others.
Watch the video
Get to know more by watching these related videos: